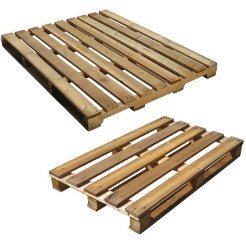
Selective pallet racking is the most common pallet racking system in use today. The type of racking system usually is completed in one of two configurations: a roll or clip-in configuration or a structural bolt-together configuration.
1. Roll Formed Selective Racking is usually manufactured in a ‘teardrop’ style. The term ‘teardrop’ is used because the holes on the column of the upright are shaped like a teardrop. Pallets rest on horizontal load beams that are held in place by mounting clips and are considered quick to access because the clips on the teardrop configurations can be easily moved and the shelves can be easily adjusted to different heights to accommodate various load sizes. As a result, roll form or clip-in configuration is convenient for a warehouse that needs to store a wide variety of product sizes as well as access product on a frequent basis.
2. Structural Pallet Racking, meanwhile, is very similar to roll formed pallet rack systems with the exception that the horizontal load beams are attached to the uprights with bolts and have much greater weight-bearing capacity. The bolt fixings consequently make this a form of adjustable shelving where racks can be constructed, reconfigured, and dismantled and reused as necessary.
Roll Formed vs. Structural Pallet Racking
Understanding how a pallet racking system can help or hurt your day-to-day operations is important. In certain circumstances roll form is the most appropriate selective pallet racking system and in other cases its structural pallet racking. Regardless of the method, however, selective pallet rack systems provide easy accessibility to all products at all times which is the major function of the concept.
If you run an operation where inventory is constantly depleted and restocked, otherwise known as ‘quick turnover’, then a selective pallet rack system is the correct approach to running your warehouse. Roll formed racking will accommodate most warehouses while structural pallet racking is an upgrade if you are dealing with high-weight situations. Another advantage to structural pallet racking is that it can be designed into the structure of the building itself, therefore making the upright columns support the roofing as well.
Popular Components of Selective Pallet Racking
Are you planning on implementing a selective pallet racking approach to your warehouse? If so make sure you are informed with these terms, considered popular components of selective pallet racking:
– Load beams (also called step beams or box beams)
– Upright frames (also called upright columns or uprights)
– Diagonal braces and horizontal braces
– Pallet supports
– Wire decking
– Footplates (also known as footpads or baseplates)
– Shims
– Row spacers
– Wall ties
– Column protectors (also known as post protectors)
– Guard rails
Construction & Safety Concerns
Because of the size and weight of pallets, there are important safety concerns you need to keep in mind not only during the planning and construction of your selective pallet racking system, but also after completion and during day-to-day operation.
1. Pay attention to any loose components in the pallet rack system, and take the time to report any damage in the pallet rack frame; such frame damage could cause the pallets to fall.
2. It is the owner’s legal responsibility to communicate this important warning to all who are around storage racks: Never climb on racks during or after assembly. Storage racks are not designed to be stepped on or climbed on. A slip or fall may result in serious injury.
3. Use only quality pallets that are not damaged. To save money, or perhaps from neglectful management, some warehouses use pallets until they become faulty and dangerous.
4. Always ensure that the proper motorized equipment is being used for the application.
5. Do not obstruct the end of aisles by staging pallets in these areas. Doing so can cause severe and potentially fatal injuries and accidents.
6. Never overload or exceed the recommended load specifications for a racking system. Overloading may cause a catastrophic failure of your storage rack system.
7. Rack audits (safety checks) should be performed on a regular basis by a qualified inspector familiar with RMI design and safety standards to make sure all aspects of system are up to 100 percent operationally safety.